High Barrier Film Laminations
High barrier film laminations are often required to protect product integrity and quality. Since 1965, Glenroy has earned a reputation for expertise in high barrier flexible packaging.
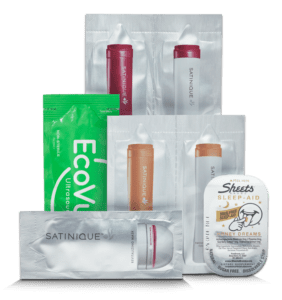
High barrier materials in flexible packaging laminations prevent the permeation of water, water vapor, oil, oxygen, aroma, flavor, gas, or light. A product’s formulation can be impacted adversely if these elements migrate into or out of the package.
Since 1965, Glenroy has earned a reputation in the flexible packaging industry for having exceptional expertise in manufacturing high barrier film laminations for “hard-to-hold” products. We provide flexible packaging for some of the hardest products to package, such as engine oils & lubricants, and even pure isopropyl alcohol (IPA).
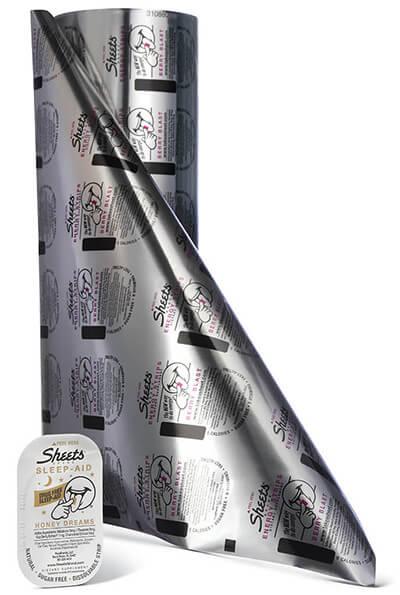
Custom-engineered Foil & Non-foil Laminations
We’re able to custom-engineer flexible packaging materials that meet stringent barrier requirements using a wide variety of specialized materials.
Foil is one of several materials used in flexible packaging that provides excellent barrier properties, and we have exceptional capabilities in manufacturing foil laminations.
We also have expertise in engineering non-foil high-barrier flexible packaging materials using sophisticated coextruded film laminations.
Looking for Barex® flexible packaging laminations?
We offer various Barex® alternatives for applications that require chemical resistance, extreme water vapor barrier, or extreme oxygen barrier. Clear high barrier Barex® alternatives are also available.
CHB (Clear High Barrier) Flexible Packaging Films
Our CHB flexible packaging films provide a cost-effective alternative to foil packaging film laminations. Features include:
- Outstanding oxygen & moisture barrier properties
- Transparent – providing optimum product visibility
- Excellent sealing characteristics
- Available with customized sealant layers for peelables, frangibles, or hermetic sealability
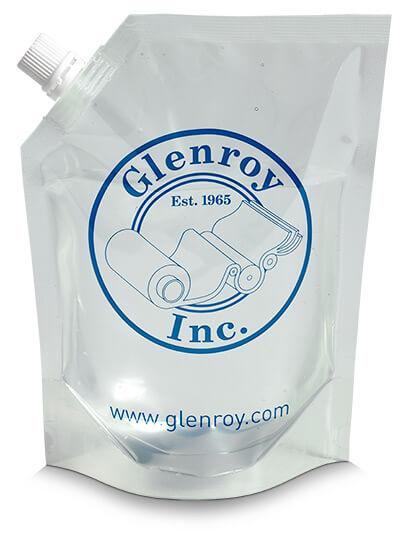
Material Selection
Structure Name | Barrier Coating | Relative Barrier | MV Barrier (g/100in2/ 24 hrs) | O2 Barrier (cc/100in2/ 24 hrs) | MV Barrier (g/m2/ 24 hrs) | O2 Barrier (cc/m2/ 24 hrs) | Relative Cost |
---|---|---|---|---|---|---|---|
CHB Bronze | PVDC | PVDC | 0.5 | 0.5 | 7.75 | 7.75 | $ |
CHB Silver | AI2O3 | AI2O3 | 0.13 | 0.13 | 2.00 | 2.00 | $$ |
CHB Gold | AI2O3 | AI2O3 | 0.065 | 0.065 | 1.00 | 1.00 | $$$ |
CHB Platinum | AI2O3 | AI2O3 | 0.02 | 0.026 | 0.3 | 0.4 | $$$$ |
Product/Package Compatibility Testing
When engineering high barrier laminations, several options should be evaluated in order to select the best flexible packaging structure. We’ll analyze the ingredients of your unique products, test various flexible packaging laminations for compatibility with your products in our on-site package engineering lab, and our experienced packaging engineers will suggest flexible packaging laminations most compatible with your products.
Learn how Glenroy helped The HopeGel Project in feeding starving children in Haiti by producing flexible packaging with an extremely high barrier against light, oxygen, and moisture.
Protecting Flavors and Aromas
Volatile or essential oils associated with aroma and flavor are usually present in minute concentrations, and retaining them can be a challenge without the right flexible packaging materials. Glenroy supplies flexible packaging for many products that require flavor and aroma retention, such as toothpastes and perfumes.
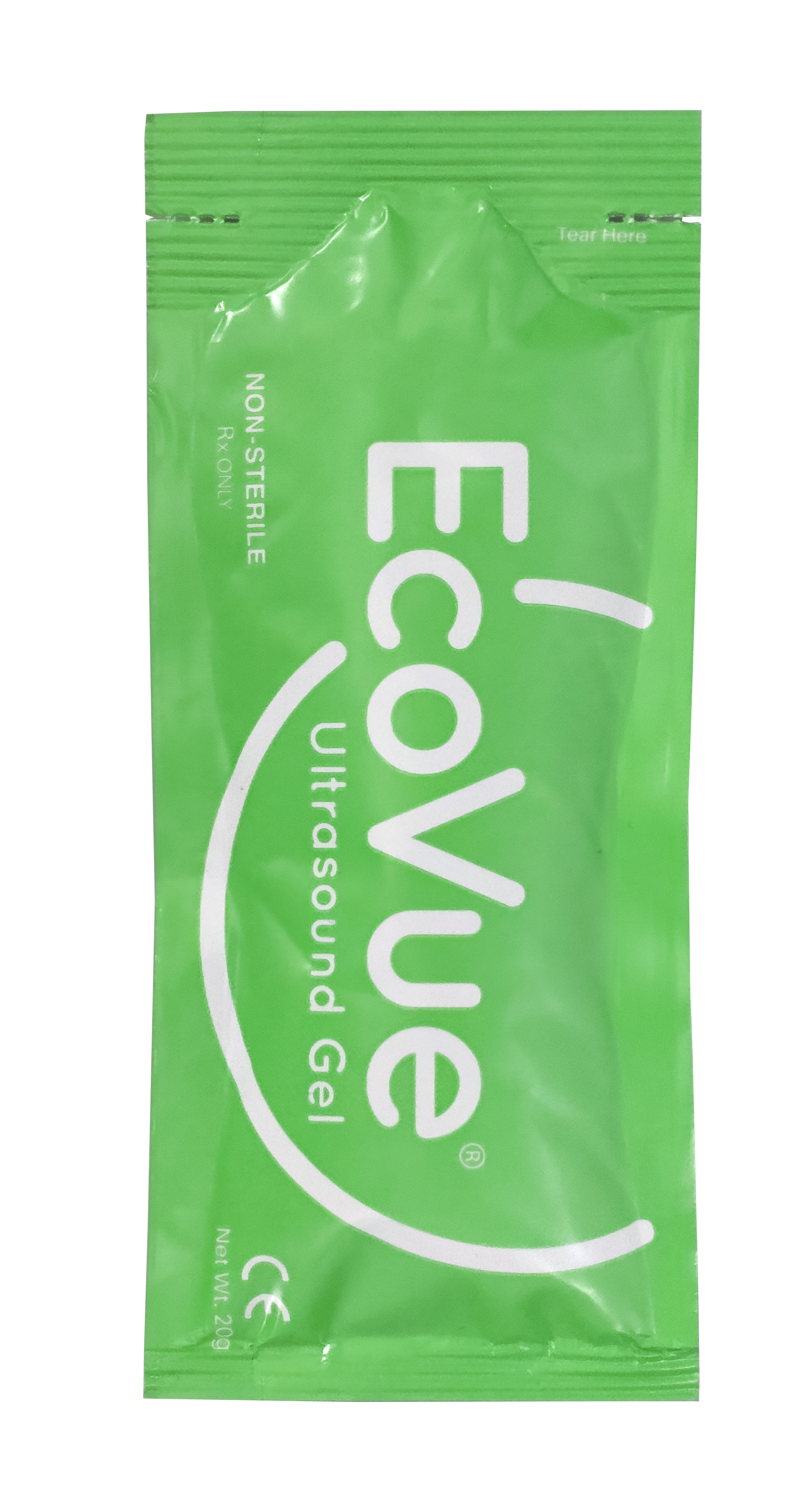
High Moisture Barrier Flexible Packaging
If you have a product sensitive to moisture, such as a medicinal or nutritional powders, we’re able to provide flexible packaging laminations with extremely high moisture barriers.
Materials used in flexible packaging have a specified moisture vapor transmission rate (MVTR). Materials such as foil, HDPE, and PVDC have excellent moisture barrier properties. We’ll work with you to custom-engineer a flexible packaging structure that will protect your products from moisture.
High Oxygen Barrier Flexible Packaging
Many products require packaging with low or virtually nonexistent oxygen transmission rates (OTR), including various products within the medical and pharmaceutical, food, or personal care markets. For example, many foods require a packaging structure that keeps oxygen out entirely in order to preserve it and extend shelf life. Without an effective oxygen barrier, the results can be changes in color, odor, taste, and overall quality.
Materials used in flexible packaging vary greatly when it comes to their oxygen barrier characteristics. Each material has an oxygen transmission rate (OTR) that specifies how much oxygen passes through the material over a 24-hour period.
Glenroy has the technical expertise to help you determine the best structure for the oxygen barrier needs your product requires.